
Pantograph Patterns and Shells
The approved Engineering Drawing Package was transmitted to Industrial Design Affiliates (IDA), a company that specialized in model making to obtain
a cost estimate for creating a Pattern and Shell for the new car. Once approved, IDA would begin the process of creating the Pattern and Shell.
The process for making the pattern and shell required great skill on the part of the model maker. The following historical slides document the major steps of the process.
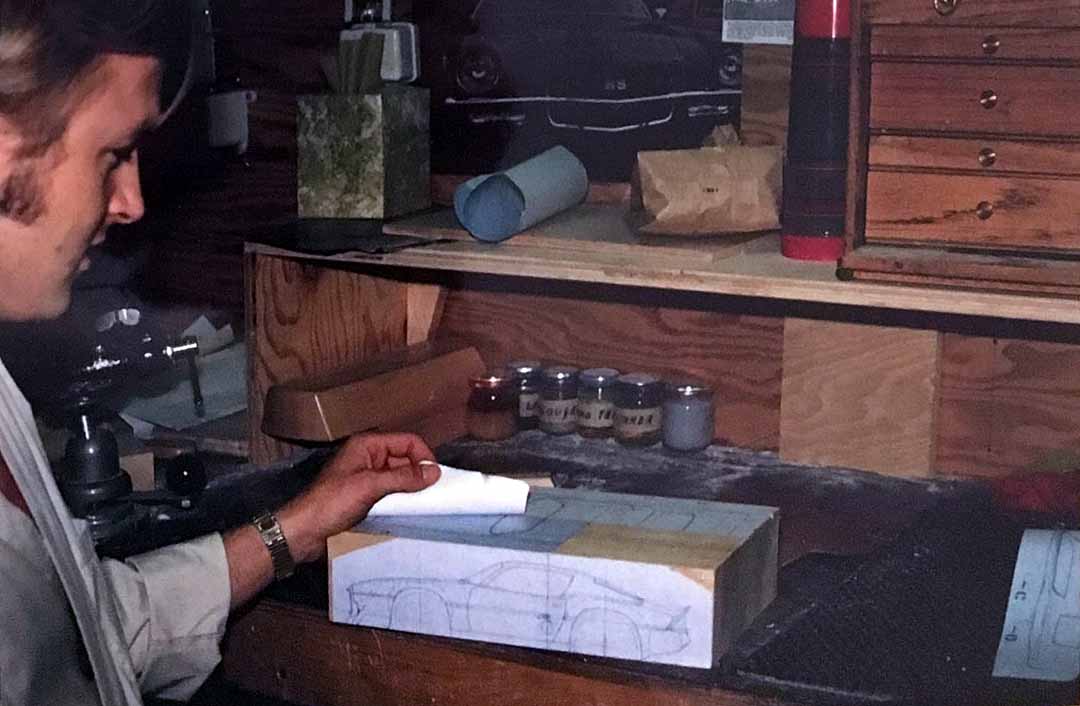
The modeler starts with a wood block. He takes copies of the engineering drawings and glues them to the faces of the block.
guide the rough cutting to get to shape of the car.

After the rough cut, more carving and the block starts looking like the car on the drawings.
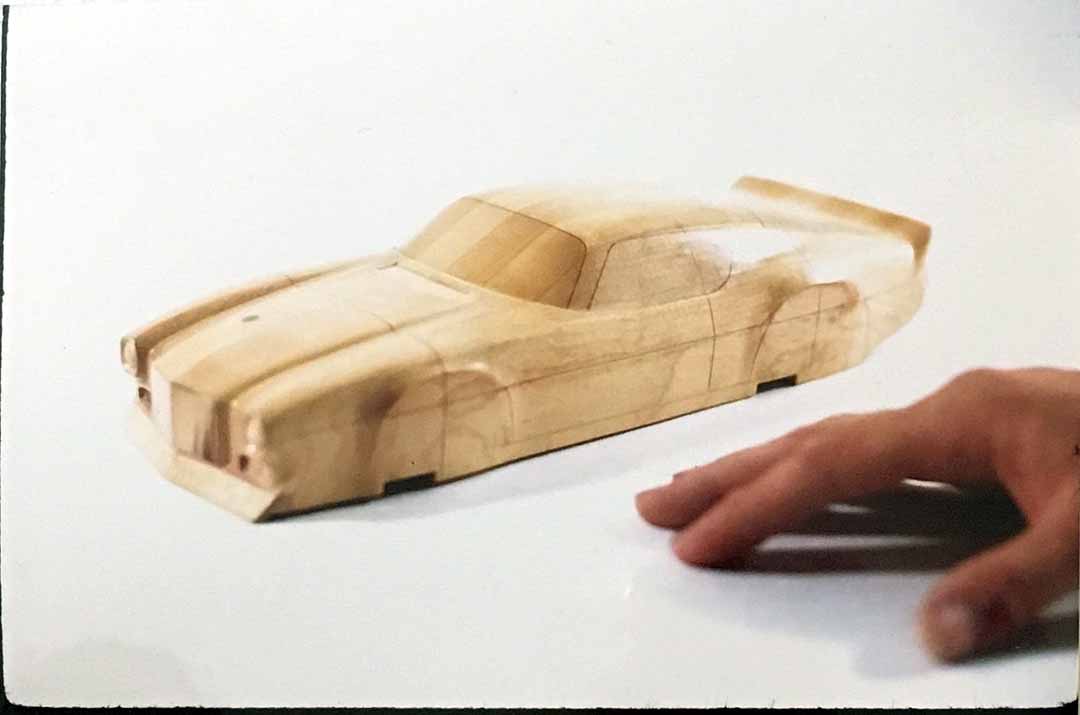
The mastery of the model maker shows as the rough cut is perfected to match the designer's concept.
The wooden model at this stage is called the "PATTERN".
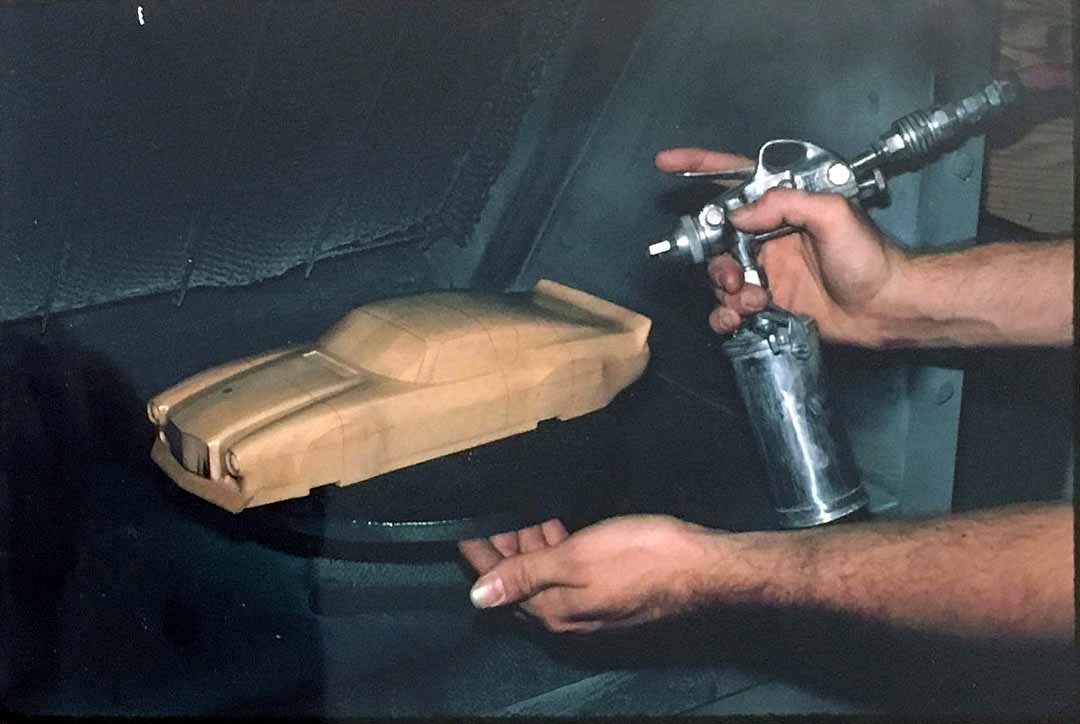
The pattern is lacquered to seal the wood in preparation for the next step.
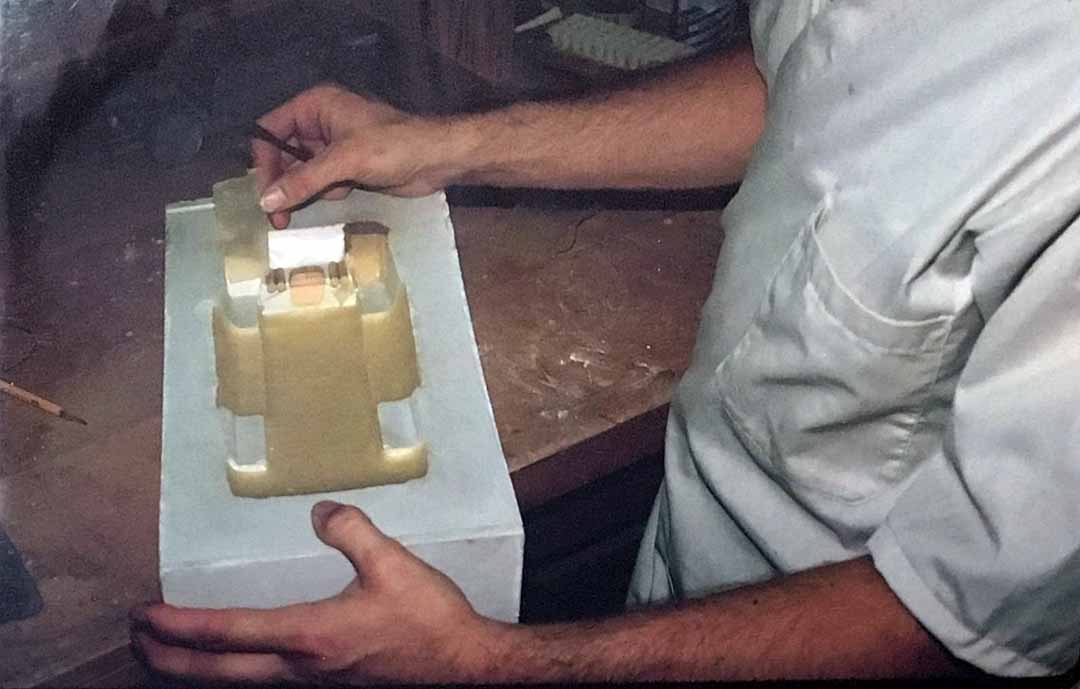
The sealed pattern is immersed in plaster of paris to create a mold.
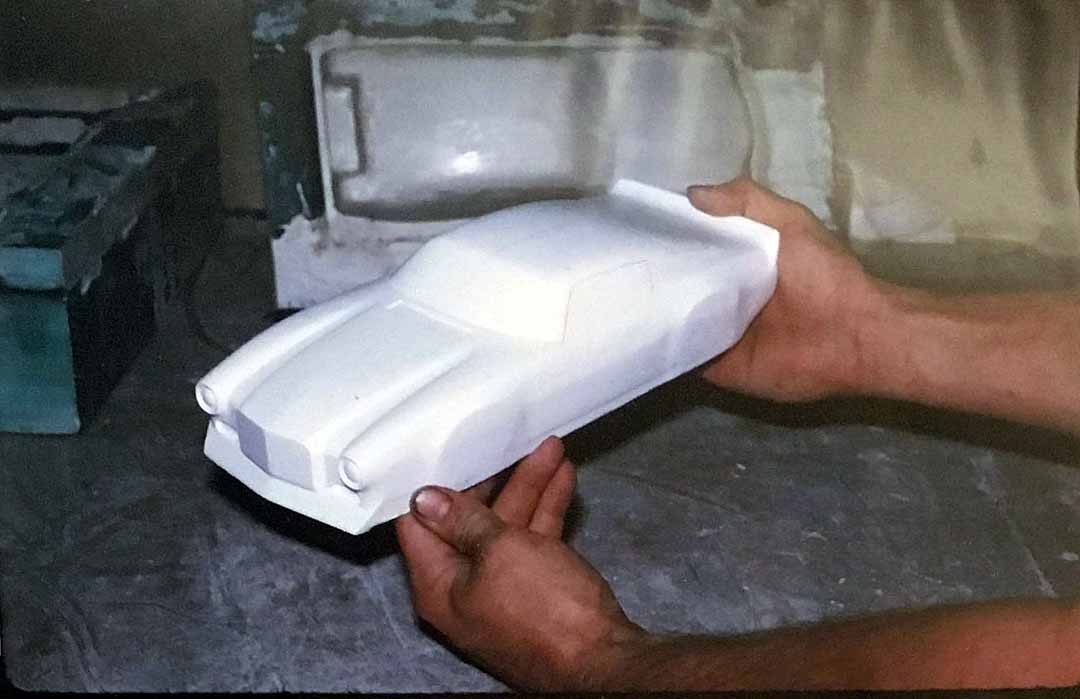
The modeler fills the mold with epoxy resin to create an exact copy of the wooden pattern. The surface of the epoxy resin is much harder than the wood pattern.
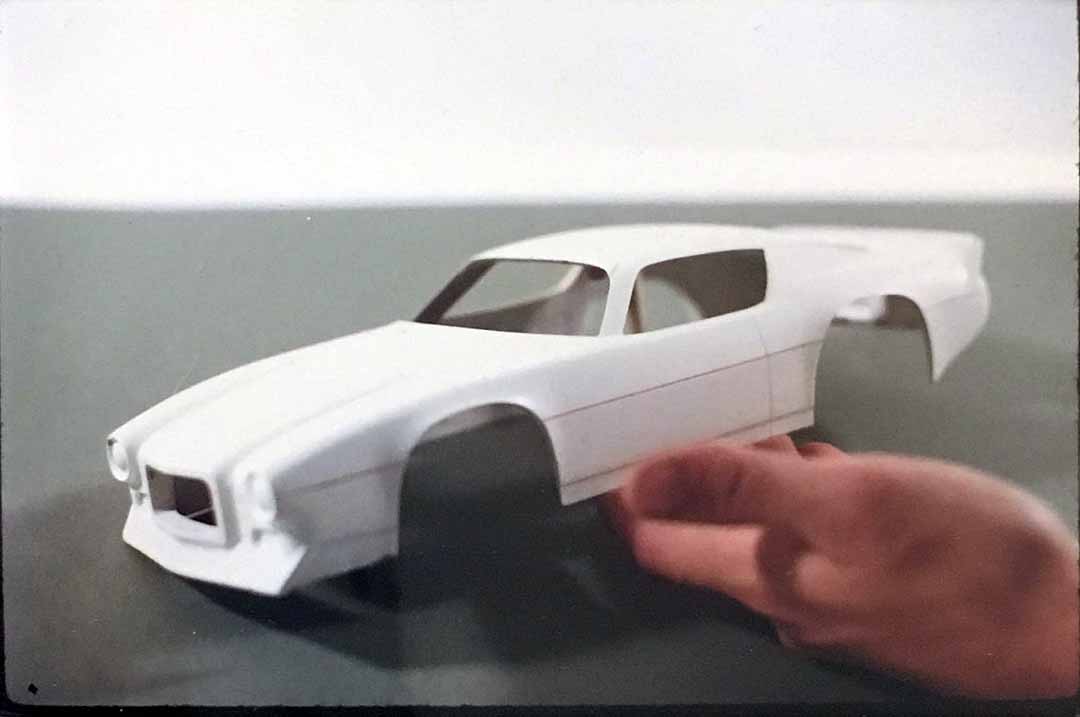
The skill and mastery of the model maker is again evident as the epoxy copy of the pattern is milled and carved to become an exact replica of
the diecast car
at a scale four times larger than the end product 1/64th scale diecast car. The epoxy model, at this stage, is called the "SHELL".
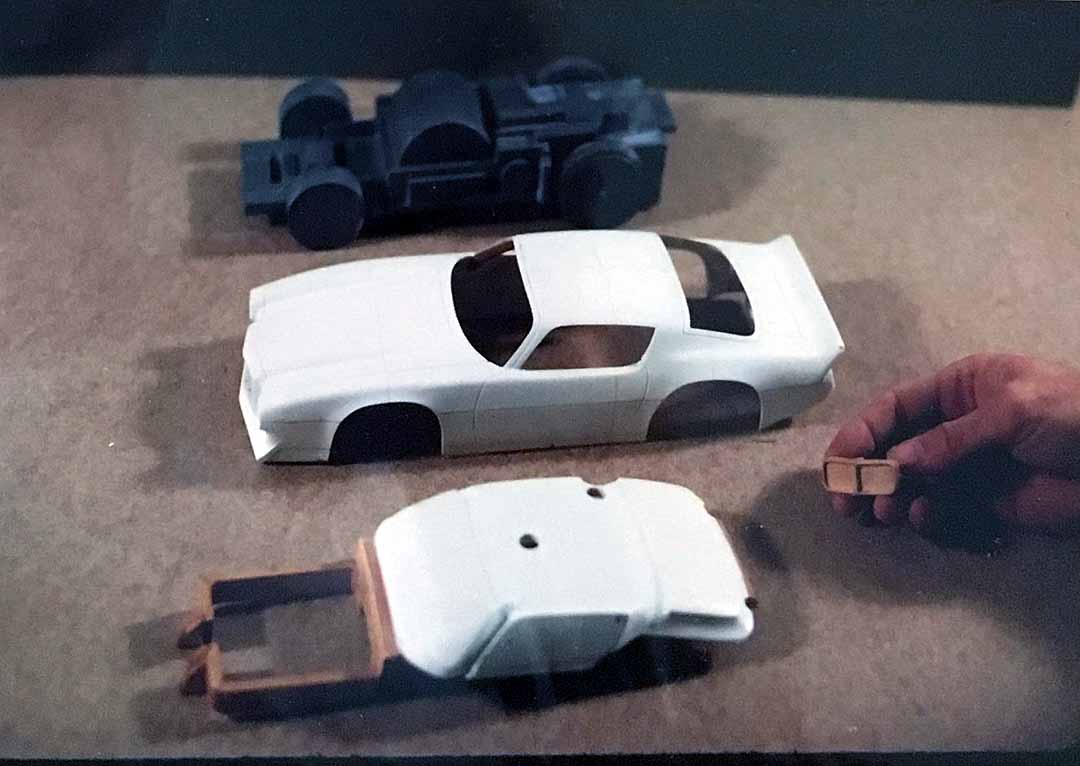
The model maker then creates a "4 Up" model of each individual piece of the car as specified in the Engineering Drawings. Sometimes, using only wood for
smaller parts and other times repeating the entire process for larger pieces such as the base or the plastic "glass".
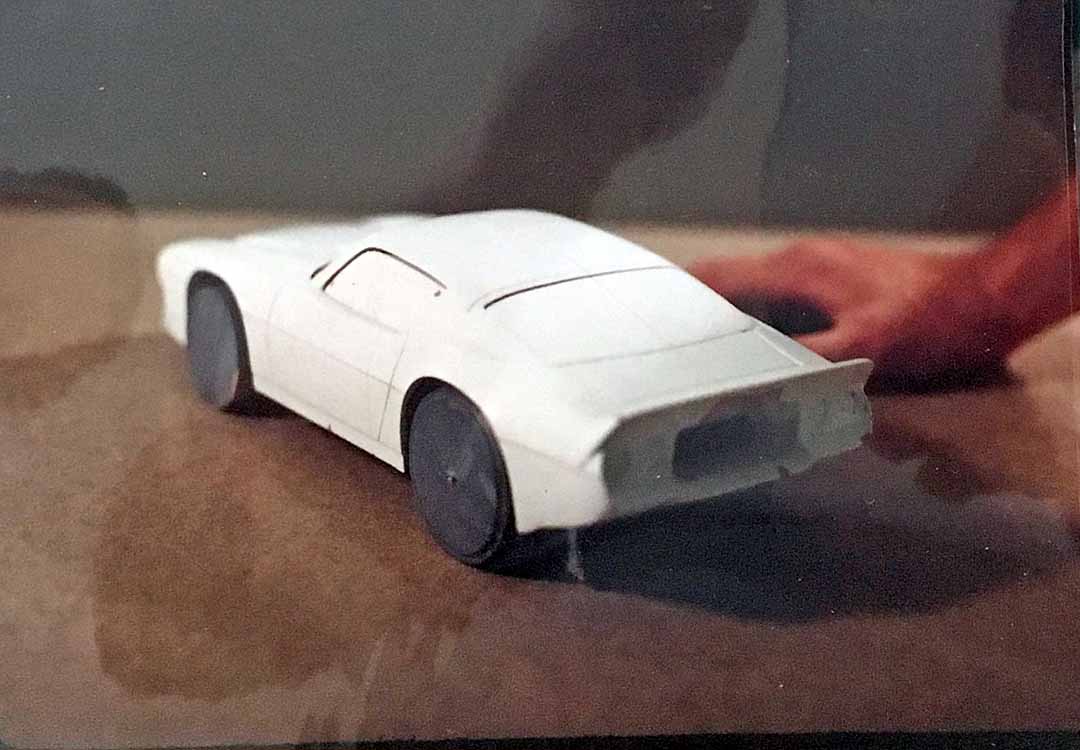
The finished Shell is then ready for the Pantograph operator to create the diecast tool and the molds for the plastic parts.
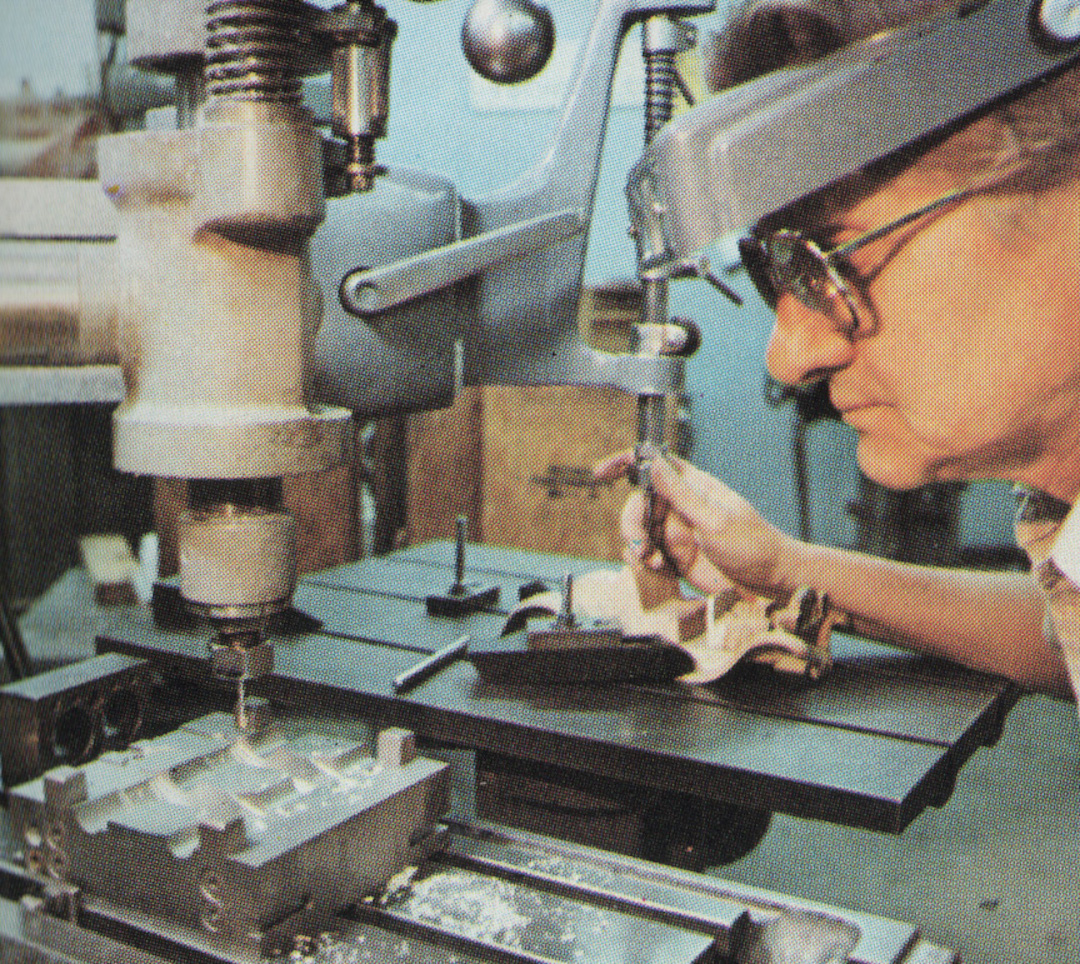
The pantograph machine and operator
The operator guides the stylus of the pantograph along the surface of the Shell. The other end of the pantograph is like a dentist's drill and mills out the metal
of the tool to create a reverse replica of the Shell. The operator may repeat the process to create multiple "cavities" in the same tool.
Click here to learn about pantograph machines.
NEXT STEP
Questions? ...
Send me an e-mail: tngray@nautiloid.net
© 2025 by Theodore N Gray All Rights Reserved.